How to Conduct a Fitness-for-Service Assessment on Your Assets
Posted on | by Metegrity Inc. | Category: Asset Integrity Management, Mechanical Integrity, Non-Destructive Testing, Inspection and Monitoring, Fitness-for-Service Assessment
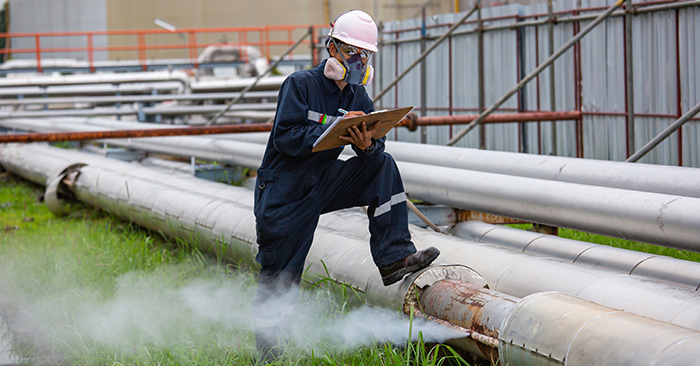
Maintaining the integrity of assets is critical to the success of any business, especially in the oil and gas industry where the failure of critical equipment can lead to costly downtime, environmental damage, and potential safety hazards. One key tool that asset integrity managers can use to assess the fitness of their assets is a fitness-for-service (FFS) assessment. In this blog post, we'll discuss what an FFS assessment is, why it's important, and how to conduct one effectively.
What is a Fitness-for-Service Assessment?
A fitness-for-service (FFS) assessment is a type of mechanical integrity analysis that is used to evaluate the current integrity of an equipment. The goal of an FFS assessment is to determine if the equipment is fit to continue operating, or if it needs to be repaired, replaced, or taken out of service altogether.
FFS assessments can be performed on a wide variety of equipment, including pressure vessels, piping systems, storage tanks, and more. They typically involve a thorough inspection of the equipment based on a detailed inspection plan. This is coupled with a detailed analysis of the results of the inspection.
Why is a Fitness-for-Service Assessment Important?
There are many reasons why conducting an FFS assessment is important. One of the primary reasons is that it can may help to prevent failures which could result in costly and dangerous accidents. By identifying potential problems before they occur, asset integrity managers can take proactive steps to address them, preventing costly downtime and potential environmental and safety hazards.
FFS assessments can also help asset integrity managers to make more informed decisions about the maintenance and repair of their equipment. By providing a detailed understanding of the condition of the equipment, an FFS assessment can help to identify the most effective and cost-efficient ways to maintain the asset's integrity, prolong its useful life, and avoid unnecessary repairs or replacements.
How to Conduct a Fitness-for-Service Assessment
Conducting a fitness-for-service assessment requires a multi-step process that involves careful planning, execution, and analysis. Here are the general steps involved in conducting an FFS assessment:
- Define the scope of the assessment: The first step is to define the full scope of the equipment assessment. This involves identifying which equipment needs to be assessed, as well as the specific parts or components of the equipment that will be evaluated.
- Gather data: The next step is to gather data about the equipment or structure. This may involve a combination of visual inspections, non-destructive testing (NDT), and other types of tests and measurements. The data collected should be comprehensive and include all relevant information about the equipment, such as its design, operating conditions, and history of use.
- Analyze the data: Once the data has been collected, it must be analyzed to determine the fitness of the equipment. This may involve a variety of calculations, simulations, and other types of analyses, depending on the specific type of equipment being evaluated. For example, an FFS assessment of a pressure vessel might involve a detailed analysis of the stresses and strains that the vessel is subjected to during normal or upset conditions.
- Determine the fitness of the equipment or structure: Based on the results of the data analysis, the fitness of the equipment must be determined. This may involve comparing the results of the analysis to established standards, such as those set by the American Petroleum Institute (API), or by developing custom criteria that are specific to the equipment being evaluated.
- Develop a repair or replacement plan: If the equipment or structure is found to be unfit for continued service, a repair or replacement plan must be developed. This plan should take into account the specific issues identified during the assessment and provide a clear course of action for addressing them. Depending on the severity of the issues, the plan may involve minor repairs, major modifications, or full replacement of the equipment.
- Implement the repair or replacement plan: Once the repair or replacement plan has been developed, it must be implemented. This may involve working with maintenance and engineering teams to make necessary repairs or modifications or coordinating the replacement of the equipment or structure.
- Monitor the asset: Finally, it's important to monitor the asset to ensure that the repair or replacement plan is successful, and that the equipment or structure remains fit for service. This may involve ongoing inspections, testing, and monitoring of the asset to ensure that it is performing as expected.
In conclusion, conducting a fitness-for-service assessment is an essential tool for maintaining the integrity of assets in the oil and gas industry. By identifying potential problems before they occur, asset integrity managers can take proactive steps to prevent accidents and failures, make more informed decisions about monitoring the condition, enhancing maintenance activities and repair scopes, and prolong the useful life of their equipment and structures. By following the steps outlined above, asset integrity managers can conduct effective FFS assessments and ensure the continued safety and reliability of their assets.
To conduct a successful fitness-for-service assessment, work with our experienced professionals at Metegrity. Our asset integrity management experts specialize in effective FFS assessments. Contact us to learn more about how we can help maintain your asset's safety and reliability.