How to Develop an Effective Corrosion Control Strategy
A 6-Step Approach
Posted on | by Metegrity Inc. | Category: Asset Integrity Management, Corrosion Control, Corrosion Risk Assessment
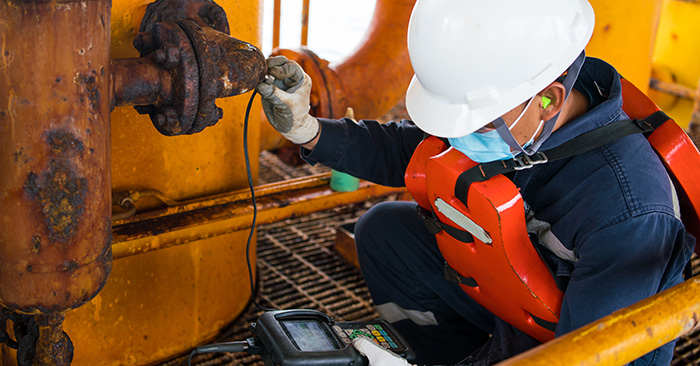
Corrosion is a natural process that affects metal components in various industries, including oil and gas. Corrosion can lead to equipment failure resulting in costly repairs and downtime, which can have significant impacts on safety, production, and profitability. Developing an effective corrosion control strategy is critical to mitigate these risks and ensure the safe and reliable operation of assets. In this article, we will discuss a six-step approach to developing an effective corrosion control strategy for the oil and gas industry.
Step 1: Conduct a Corrosion Risk Assessment
The first step in developing an effective corrosion control strategy is to conduct corrosion risk assessments. This involves identifying the types of corrosion that are likely to occur in the specific operating environment, the rate of corrosion, and the impact of corrosion on equipment and operations. The assessments should also consider factors such as temperature, pressure, fluid flow, and the presence of corrosive agents, such as hydrogen sulfide.
Step 2: Define Corrosion Control Objectives
Once the corrosion risk assessments have been completed, the next step is to define corrosion control objectives. These objectives should be specific, measurable, achievable, relevant, and time bound. For example, the objective may be to reduce the rate of corrosion to an acceptable level within the next 12 months. Defining clear objectives will help to ensure that the corrosion control strategy is focused and effective.
Step 3: Select Corrosion Control Measures
The next step is to select corrosion control measures that are appropriate for the specific operating environment and corrosion risks. There are many corrosion control measures available, including coatings, cathodic protection, chemical inhibitors, and material selection. The choice of the appropriate corrosion control measures will depend on factors such as the type of corrosion, the severity of the corrosion risk, the cost of the measures, and the impact of the measures on operations.
Step 4: Develop a Corrosion Management Plan
Once the corrosion control measures have been selected, the next step is to develop a corrosion management plan. The plan should outline the specific measures that will be implemented, the timelines for implementation, and the responsibilities for implementing and monitoring the measures. The plan should also include contingency measures in case of unexpected corrosion events.
Step 5: Implement Corrosion Control Measures
The next step is to implement the selected corrosion control measures according to the corrosion management plan. This may involve applying coatings to equipment, installing cathodic protection systems, adding chemical inhibitors to fluids, or selecting corrosion-resistant materials. The implementation of the corrosion control measures should be closely monitored to ensure that they are effective in reducing corrosion rates and minimizing the risk of equipment failure.
Step 6: Monitor and Evaluate Corrosion Control Effectiveness
The final step in developing an effective corrosion control strategy is to monitor and evaluate the effectiveness of the corrosion control measures. This involves collecting data on corrosion rates, equipment performance, and maintenance costs, and analyzing this data to determine whether the corrosion control objectives have been met. If the corrosion control measures are not effective, the corrosion management plan may need to be revised, and additional measures may need to be implemented.
Contact us now to develop an effective corrosion control strategy for your business and mitigate the risks of equipment failure, downtime, and costly repairs.
Keep Reading
How to Leverage AIM for Pipeline Corrosion Control
How to Leverage Integrity Operating Windows for Improved Corrosion Control